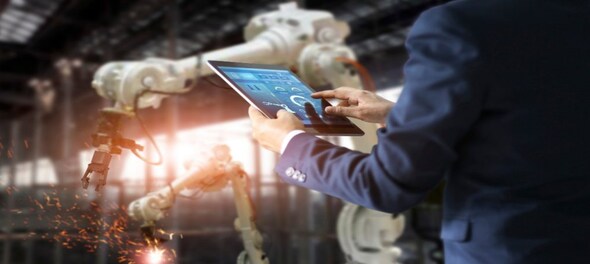
Conducting business in this VUCA world has never been so challenging for the manufacturers. Globally, the industry is being impacted by various trends and repercussions of the novel coronavirus. Not only must they deal with the market volatility but should also adapt to an ever-changing cohort of next-generation technologies such as IoT, Automation, Digital Twin, Industry 4.0, Deep learning-based analytics, and more. These technologies aim to drive smart manufacturing, connectivity, and streamlining of operations, making supply chains more resilient and unlock the potential for data-driven top-line and bottom-line growth. Adoption and ubiquitous presence of such technologies in autonomous cars, traffic alert and collision avoidance systems in aircraft, autonomous hauling system with advanced sensors, GPS, and image recognition systems to conduct operations inside the mine sets the benchmarks and create exemplars of what is the art of the possible for inclusion of such technologies in manufacturing operations.
Since IoT technology has introduced innovative uses cases in the manufacturing industry, the tools to implement it have become affordable in the past five years. According to a report by Microsoft, the average cost of a sensor dropped nearly 200 percent to an average price of $0.44 between 2004 and 2018, making intelligent manufacturing more accessible and inexpensive. With technical modernisation, and ever-dropping cost curves, manufacturers can optimise critical control points of operations depending on the specifications of product manufactured. Manufacturers are hence exploring more ways to bring about the benefits of digitalisation without increasing their OPEX. They are focused on converging IT (Information Technology) and OT (Operational Technology) to drive innovation across the manufacturing setup and the corporate office. Moreover, they are looking at cost-effective opportunities to revamp several manual processes, like a modern manufacturing factory.
The overarching construct of digitalisation for any manufacturing plant should be thought of on the basis of the manufacturing process that is used for the products
With advanced technology, manufacturers can automate and monitor such processes in real-time. Also, they can regulate minimum deviation from set points with MIMO (Mulitple Input and Multiple output) Advanced control systems based on dynamic models of input-output process models. Manufacturers can design L2 and L3 systems for robust set-point tracking and disturbance rejection. They can technically advance PLCs to stream data into the operations network through OPCs (Open platform communications) for feedback and analysis. The design of such a manufacturing setup is based on theoretical simulations made on heat, material balances, and empirical data, ensuring stability, energy optimisation, quality of end-product, and inventory control.
The ubiquity of next-generation technologies is driving the evolution of manufacturing worldwide. From shop floor automation to virtual monitoring of boilers, manufacturers have realized the importance of digitalization. However, to ensure its successful implementation, manufacturers must strategically think and prepare a deployment roadmap.
The following are some key considerations that will help manufacturers adopt digitalization and maximize their results effectively.
Authored by Saurabh Bhatnagar, Consulting, Partner, EY India. The views expressed are personal.
Check out our in-depth Market Coverage, Business News & get real-time Stock Market Updates on CNBC-TV18. Also, Watch our channels CNBC-TV18, CNBC Awaaz and CNBC Bajar Live on-the-go!


BJP is planning to ban RSS, says Shiv Sena (UBT) chief Uddhav Thackeray
May 18, 2024 8:01 PM
Punjab Lok Sabha elections: Complete list of Congress candidates
May 18, 2024 4:08 PM
Punjab Lok Sabha elections: Check full list of AAP candidates and constituencies
May 18, 2024 12:59 PM
PM Modi, Rahul Gandhi election rallies in Delhi today: Here are the routes to avoid
May 18, 2024 11:28 AM