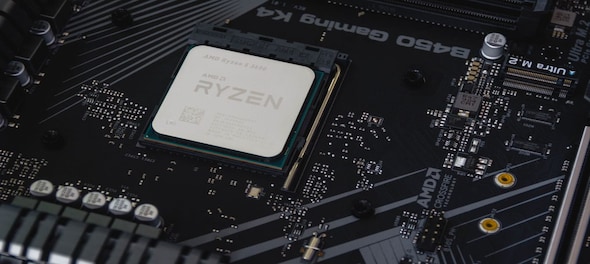
In January, passenger vehicle (PV) sales witnessed a YoY decline of over 4 percent as semiconductor shortage bruised the segment, automobile dealers’ body FADA said on Tuesday.
FADA president believes the industry misjudged demand post-lockdown. Moreover, chipmakers moving to electronics and server industries are resulting in slow production, he added.
"Industry's underestimation of post-pandemic rebound along with chipmakers prioritizing higher-volume and more lucrative consumer electronics market has created a vacuum for semiconductors," FADA president Vinkesh Gulati noted.
This is not a one-off case. In a meeting with automakers and chip makers, the Chinese industry ministry asked the latter to ease the supply shortage that forced automakers across the world to halt production.
Semiconductor chips are chips made using the semiconductor Silicon. These chips control memory functions in products ranging from automobiles, computers, gaming consoles, and other electronic items. These chips were on the front-seat as our cars became digitalised with Bluetooth connectivity and driver-assist functions, navigation, and hybrid-electric systems. The shortage in these chips that enable our cars has hit the sector particularly hard.
Automakers from General Motors to Stellantis and Honda Motors are shutting assembly lines due to the shortages, while some firms have furloughed staff.
Beyond cars
Semiconductor chips played a major role in the evolution of computers. From a room-sized machine to a system that sits on our lap – this degree of transformation was possible by the discovery of silicon and the lucrative ways in which humans could use them to power their day-to-day functions.
Naturally, due to their sheer versatility, the chips are found almost everywhere. From the device, you are reading this article from, to the car you drive. However, this versatility is why its shortage is on the verge of taking down more than one industry.
Background
The trouble began in 2020 with a virus taking the globe by surprise. Lockdowns and travel restrictions coupled with stimulus checks prompted shoppers from across the world to spend on electronics, which in turn, fuelled demand for chips. Many of these products — think, latest Xbox series, PlayStation 5, and Chromebook laptops — are either sold out or subjected to delayed shipping.
Apple, another major chip customer, recently said a shortage of some components cut down sales of some new high-end iPhones.
In months, a demand that brought good news for chip manufacturers sowed seeds of a potentially severe shortage in auto, smartphone, and TV industries.
"It is difficult for us to increase the production of the PS5 amid the shortage of semiconductors and other components. We have not been able to fully meet the high level of demand from customers (but) we continue to do everything in our power to ship as many units as possible to customers who are waiting for a PS5," said Hiroki Totoki, CFO, Sony.
How is the car industry faring?
Two words: not good. US car giant General Motors have shut down three of its manufacturing plants.
"Semiconductor supply for the global auto industry remains very fluid," the company said in a statement. "Our supply chain organisation is working closely with our supply base to find solutions for our suppliers’ semiconductor requirements and to mitigate impacts on GM."
Honda UK shut down its plants for several days due to chip shortage. Ford and Volkswagen are also cutting production and shutting plants as they wait for the supplies to pick up.
Toyota has halted four of its production lines in Japan due to shortage. It is also cutting the production of its full-size pick-up truck, Tundra. Nissan has also announced cutting production on one of its plants in Japan.
Subaru has already shut its main Gunma factory and its other plants in Japan.
Why is the car industry hit so badly?
Cars use semiconductors in everything – from powering steering wheel to entertainment systems and parking cameras. So, if one chip that powers your steering wheel gets delayed, then so will the rest of your vehicle, Bryce Johnstone, director of automotive segment marketing at chip designer Imagination Technologies, told CNBC via email.
The shortage began as the world moved into the second quarter of 2020, Falan Yiung, director of industry statistics and economic policy at Semiconductor Industry Association said.
In March and April, as automakers shut down factories, the demand for automotive chips tanked. Simultaneously, as demand in serve and electronics industries charged up, semiconductor firms refocused their efforts.
Fast forward to a couple of months, and the demand for automotive semiconductors rallied quicker than the industry anticipated. So much so that Q4 auto sales YoY were positive worldwide.
Semiconductor industries tried ramping up their production to meet this unanticipated demand. But as Yiung told CNBC, "One cannot remedy the supply-demand imbalance with the flip of a switch.”
Semiconductor manufacturing is one of the most complex manufacturing processes, he said. The industry has the lead time of over six months – which, otherwise is normal. But when so many players from different sectors are rushing to meet rising demand, 26 weeks becomes one of the biggest challenges.
Semiconductor industry does not have enough competition. Mostly because only a couple of companies can build the smallest chips – the game. Currently, only Samsung and TSMC have a working knowledge to manufacture the latest 5 nm chips on a commercial level.
When the chip industry has to decide between auto, telecom, and the server industry – it chooses the latter. With high gross margins, the server industry is a lucrative choice for them.
Analysts believe automakers’ cost-consciousness have put them in such a tight spot. These issues stem from their just-in-time production methodology and their incredibly complicated supply chains, Johnstone added.
The just-in-time methodology is an inventory management strategy that aims to increase efficiency by reducing inventory costs. In simpler words, firms using this strategy produce their goods, only when they anticipate demand. This helps them minimize unnecessary inventory cost. For its success, the producers have to be spot-on with their demand forecasting with reliable suppliers. And as we have seen, that was not the case.
How are chip makers faring?
An interesting question to ask since no one wants to lose business. According to a Reuters report, the Asian chipmakers are rushing to expand their production capacities to meet the global demand. However, many have warned it would take months to plug the supply gap as they struggle to keep up with the strong demand.
However, some chipmakers are battling issues like under-investment. Some Asian makers manufacture eight-inch chip – an old and less sophisticated version – and supply them to automakers. Such manufacturers are under strain.
“We are under great pressure now,” said Zhao Haijun, co-CEO of China’s top chipmaker Semiconductor Manufacturing International Corp, which last week announced plans to expand capacity by 45,000 wafers per month at its 8-inch fabrication plant this year.
One way to boost capacity is by decreasing the lead time to procure equipment. Lead time is the amount of time taken to complete a process; in this case, acquiring equipment offshores. However, the sanctions imposed by the Trump administration have caused supply chain disruptions that are hard to battle.
TSMC, the world’s top contract chipmaker, will increase its capital spending on production of advanced chips to about 60 percent YoY. At the same time, United Microelectronics Corp (UMC) will increase the expenditure to over 50 percent.
The basic rule of economics defines increasing demand and decreasing supply results in a price hike. Unsurprisingly, UMC expects overall chip prices to rise as much as 6 percent this year. Renasas, another electronics corporation, is looking at a 15 percent increase in auto chips, and 10-20 percent price rise in other chips.
(With inputs from agencies)
(Edited by : Jomy)
Check out our in-depth Market Coverage, Business News & get real-time Stock Market Updates on CNBC-TV18. Also, Watch our channels CNBC-TV18, CNBC Awaaz and CNBC Bajar Live on-the-go!


I.N.D.I.A. bloc committed to predictable and stable tax environment: Jairam Ramesh
May 21, 2024 6:33 PM
Exclusive | INDIA bloc will ensure stable policy framework, simple GST, end tax terrorism: Jairam Ramesh
May 21, 2024 5:02 PM
Cong leaders 'failed' to protect party's constitution says FM Nirmala Sitharaman in Bihar
May 21, 2024 4:01 PM
Who will succeed Modi? Oppn thinks Amit Shah will, but PM said this
May 21, 2024 2:38 PM